INDUCTION - Electronic
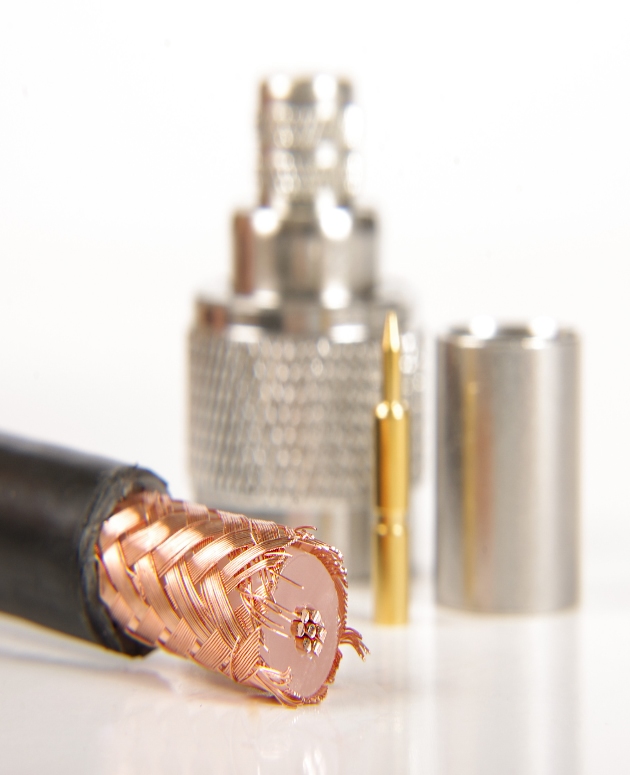
Tinning RF cable to connectors - A rapid and precise solution
Eliminate defects and enhance the quality of electrical connections with induction tinning. A solution to ensure durable and flawless connections.
Induction tinning of cables to connectors is a crucial process for ensuring reliable and high-quality electrical connections. Traditional methods can lead to issues such as uneven tinning, rework, and time loss. Adopting induction technology provides precise temperature control, reducing defects and enhancing the overall quality of connections. This approach not only optimizes efficiency but also ensures consistent repeatability, regardless of cable size.